What To Do During and After a Difficult Regulatory Inspection
My second June article guides you through an existential crisis for your company.
BONUS: I host a live chat in Substack every Friday at 9am PST. This is exclusive to my Substack subscribers! Questions? Don’t hesitate to reach out.
Regulatory inspections are a regular occurrence for drug and medical device CROs, CMOs, and clinical trial sites. The Office of Inspections and Investigations (OII) leads these activities within the FDA. If your company produces research or products for international use, you may also be visited by inspection teams from global regulatory authorities. The FDA visits follow publicly available procedures [1], and your company should have a policy and program in place to follow. Nevertheless, an inspection can be stressful, more so when it does not seem to be going well. How you respond in these situations can make a significant difference in the outcome. Let’s look at the steps you should follow to ensure a positive outcome. This outline will follow an inspection process for a drug manufacturing plant. I’ll refer you to the Office of Inspections and Investigations website [2] for details on inspections for other areas under the FD&C Act.
Document the Inspection
When an FDA investigator arrives at your site, they will present their credentials and a Notice of Inspection (Form 482). The inspectors will examine your processes and look at records, and they may collect samples. Quite often their first request will be a dock to stock tour of your facility. Your procedures should have previously designated knowledgeable persons to accompany the investigators at all times, along with notetakers to create written records of the discussion and any requests for information. Other company personnel and resources should be assembled to produce copies of requested records and other information. Document everything the investigators see and read, and every conversation they have with personnel. Site leadership are expected to debrief with Quality leadership every day to stay informed about the progress of the inspection and discuss immediate actions where appropriate. At the conclusion of the inspection, the investigator will discuss any significant findings or concerns and leave them with a report of any objectionable conditions or practices (a Form 483). The report’s purpose is to guide your firm’s management on corrective actions.
You should always expect to receive some observations, since no plant is perfect. It gets more complicated when the list of observations runs to multiple pages and covers several quality systems. This is a sign that your quality management systems are not working well. This situation is quickly evident in the level and subject of questions from the investigators. If the records you provide to confirm your policy and program SOPs aren’t satisfying them, they will ask for more detail. That’s a signal they believe an observation may be appropriate. Leadership should take time to meet after each day’s debrief meeting to assess the situation and bring in more resources as needed.
Organize Your Response
Start working on your Form 483 response while the inspection is in progress by nominating team leads for each expected observation. These personnel can start investigations and uncover documentation that may convert a critical observation to a minor one or remove it entirely from the list. Add members to each team based on the observation’s severity and give them the mandate to dedicate themselves to the response. You have a timeline and expectations to meet (see the next section); more than one company has found themselves with a warning letter due to leadership failing to back up the response team with authority.
I don’t advocate making hasty changes unless an immediate action addresses a critical defect and is consistent with how you normally handle a deviation. It’s better to conduct a full root cause investigation and base your actions on the full spectrum of evidence. Try to find all the warts – those not associated with an observation can be added to a prioritization list for your internal audit program (see Plan Ahead below). It’s a good idea to review that program for observations made and CAPA opened prior to the inspection, because they show you were paying attention without the inspector’s prompts. Be prepared to make hard choices – better to stop production than waste time and materials on batches that can’t be released.
Meet your timelines
There’s no prize for submitting your response early, but there is a reward for getting the content and tone right. You have 15 working days to respond to your Form 483, and you may request an extension during that time frame to prepare a more detailed response. I recommend taking the full 15 days to investigate, document, and craft your responses. As has always been true, giving a completed document a day to sit before the final proofreading will give you a fresh perspective from which to spot discrepancies.
Your objective should be to calmly and confidently respond to each observation using clear, jargon-free language and structured organization. Explain your response in detail and provide hard data, test results, and any other evidence that supports your claim. Be crystal clear about what you intend to do to resolve each observation. Distinguish between corrective and preventive actions. Where you are disputing an observation, provide abundant proof to substantiate your position. Preliminary drafts of each response point should be available throughout the process for leadership review and feedback. Open an umbrella CAPA in your QMS and create linked CAPA plans for each observation. You’ll use these CAPA to track your progress and provide updates to the regulatory body.
Show Leadership
It’s not possible to hide the fact that regulators have arrived for an inspection, so don’t try. Instead, have a respected leader prepare and send regular communications, and back them up with floor appearances to back up team leaders. Rumors will fly; address them with facts. Mid-level leadership should chat daily with team leads to answer questions and provide support. No operator should be interviewed without a knowledgeable person from their leadership chain being present for support. Inspector interviews are opportunities to observe knowledge, skills, and abilities that may be underappreciated in the day-to-day routine. Take note for the next performance discussion!
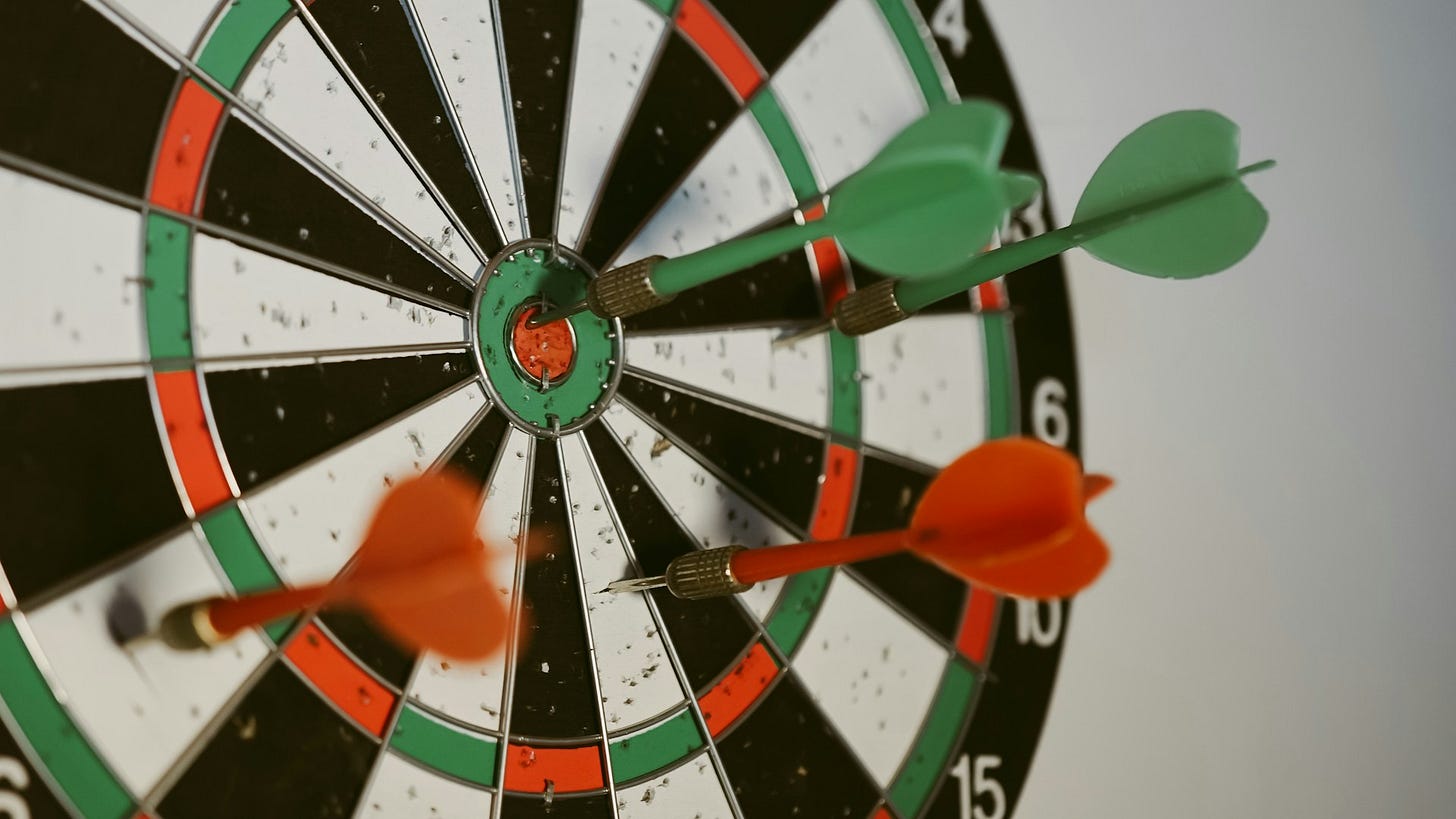
Celebrate the Wins
When an inspection ends with a detailed Form 483, it can be easy to catastrophize. Instead, review the daily debrief notes and find instances where the team’s immediate response demoted or removed an observation from the potentials list. Celebrate these conversions as successes. Acknowledge the work done so far, and thank everyone, whether they were an active participant or not. A successful inspection starts on the shop floor with engaged employees mindful of how their work contributes to a safe and efficacious final product.
During response preparation and after submission, keep everyone informed about your progress and confidence. Good CAPA involve many participants – create opportunities to briefly celebrate when each is completed. A company-level progress bar will help keep everyone focused on the goals. It takes time for an inspection to be completed and classified. When yours comes back with a VAI (voluntary action indicated) outcome, celebrate loudly and long. A mature quality management system is hard to build and takes sustained effort on everyone’s part. Don’t miss the opportunity to recognize and honor this team effort because its no small thing.
Plan ahead
This always feels like a section that belongs at the beginning. However, most companies fail to create a robust inspection program before they experience one. Be aware that the FDA can schedule an inspection immediately after you register your establishment. Set up your policy, program, and procedure documents before then and subject them to a mock inspection (outside consultants are perfect for that role). A routine internal inspection program is essential to identify gaps before deviations or inspections occur. Observations made and CAPA opened within the internal inspection program are outside the scope of an inspection. Out-of-scope issues identified during a 483 response should be evaluated and prioritized within your internal program. Create and implement a routine risk-identification and prioritization system across the plant.
Education on and monitoring of the processes and procedures used by the regulatory agencies is a key element of inspection preparedness. Freshen up your training with updated content on topics like the purpose of inspection-readiness, what to do when the inspectors arrive, or how to conduct yourself during an investigator interview. Challenge promotion-ready personnel with short assignments to research best practices, common observations, and support internal audits. Translate their work into your processes and training and publicly acknowledge their efforts.
The Take Home
A successful inspection only results from a mature quality management mentality. Building that takes intentional planning and activity, all of which is available to companies of any size. I’ve observed companies large and small fail miserably and suffered the consequences. Follow these guidelines to prepare and respond, and you’ll be among the companies setting the standards of the future.
References
[1] USFDA website, Investigations Operations Manual. Accessed May 28, 2025. https://www.fda.gov/inspections-compliance-enforcement-and-criminal-investigations/inspection-references/investigations-operations-manual
[2] USFDA website, Inspections, Compliance, Enforcement, and Criminal Investigations. Accessed May 28, 2025. https://www.fda.gov/inspections-compliance-enforcement-and-criminal-investigations
[3] USFDA website, What should I expect during an inspection? Accessed May 28, 2025. https://www.fda.gov/industry/fda-basics-industry/what-should-i-expect-during-inspection
Other Resources
The FDA has a wealth of resources about inspection procedures. Here’s a short selection to whet your appetite.
USFDA website, CDER Manual of Policies and Procedures (MAPP). Accessed May 28, 2025. https://www.fda.gov/about-fda/center-drug-evaluation-and-research-cder/cder-manual-policies-procedures-mapp
USFDA website, Inspection Guides. Accessed May 28, 2025. https://www.fda.gov/inspections-compliance-enforcement-and-criminal-investigations/inspection-references/inspection-guides
USFDA website, Inspection References. Accessed May 28, 2025. https://www.fda.gov/inspections-compliance-enforcement-and-criminal-investigations/inspection-references
USFDA website, Regulatory Procedures Manual. Accessed May 28, 2025. https://www.fda.gov/inspections-compliance-enforcement-and-criminal-investigations/compliance-manuals/regulatory-procedures-manual
USFDA website, OII FOIA Electronic Reading Room. Accessed May 28, 2025. https://www.fda.gov/about-fda/office-inspections-and-investigations/oii-foia-electronic-reading-room
USFDA website, FDA Form 483 Frequently Asked Questions. Accessed May 28, 2025. https://www.fda.gov/inspections-compliance-enforcement-and-criminal-investigations/inspection-references/fda-form-483-frequently-asked-questions
USFDA website, Compliance Program Manual. Accessed May 28, 2025. https://www.fda.gov/inspections-compliance-enforcement-and-criminal-investigations/compliance-manuals/compliance-program-manual
Thanks for reading Thinking Kat! You can help me by liking this post, becoming a paid subscriber, or sharing this publication with your friends.